CLICK LINKS/PICTURES BELOW FOR MORE INFORMATION
Category: Uncategorized
FIBERMAK Fiber Optic Laser Cutting Machine
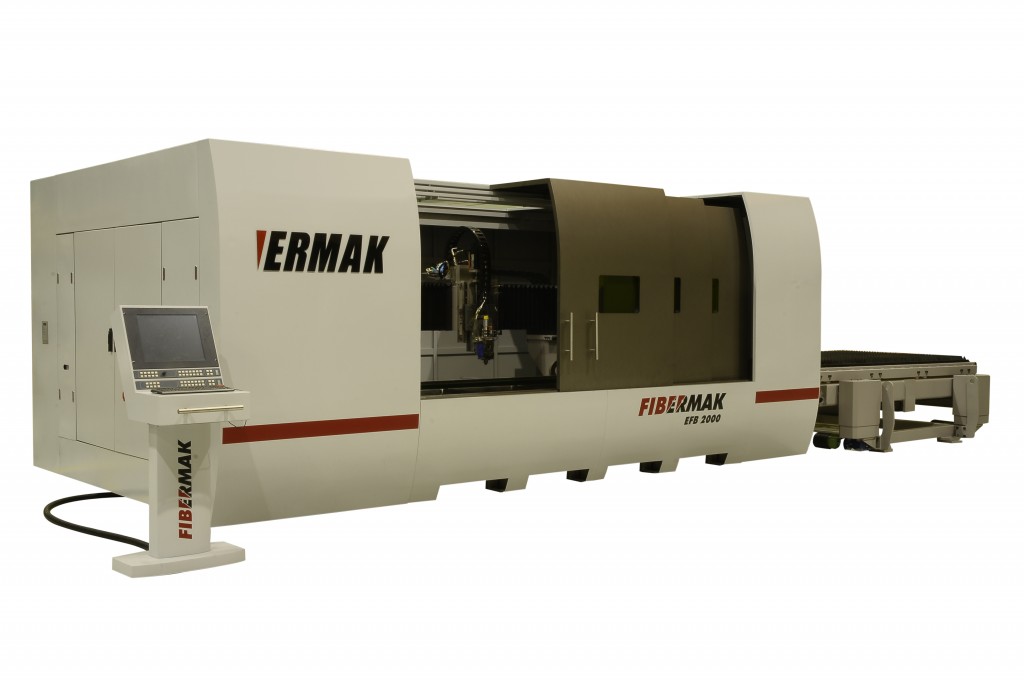
- Strong design,
- Ultra low energy consumption,
- Fast cutting capacity and
- Almost zero maintenance cost.
- 1/2″ mild steel, 1/4″ stainless steel cutting capacity.
FIBERMAK transmits the laser beam onto the sheet metal by fiber cables and its cutting quality with high beam density is perfect on thin sheets compared to other alternatives. Fiber optic laser cutting technology proves high quality cuttings at very fast speeds. The energy consumption is 70% less compared to CO2 lasers. You’ll also benefit from easy cutting of reflecting materials such as aluminum, copper, brass etc. via low wavelength depending to its working principle.
WHY FIBERMAK?
- 60% – 100% faster compared to other laser cutting machines. Axes equipped with Bosch – Rexroth linear motors and drivers reach to 472 IPM speed and accelerations are 2 G on Y, 1,5 G on X axes.
- Cuts thin materials 3 times faster compared to CO2 lasers and energy consumption is simultaneously lower.
- 70% energy savings by fiber optic laser technology is plant friendly.
- Because of diode technology there is no need to laser-mix gas used at CO2 laser cutting machines.
- Because laser transmitting is done by fiber cable there is no need for optical components such as beam path, folding mirror and quartz tube etc.
- You can make production 24 hours a day
- Part cost savings up to 50%.
- You can prevent from production faults by automation at your premises.
- You save from molds and apparatuses.
- Possible to cut reflecting materials such as aluminum, copper, brass etc. precisely and by smooth surface quality.
- FIBERMAK has strong frame, equipped with worldwide well known, long life, quality components and designed to work accurately and continuously even at hard conditions.
ROFIN RESONATOR
- ROFIN FL Series high brightness lasers.
- The emitted wavelength in the range of 1 μm achieves high absorption in many materials.
- FL Series Laser allows all common solid-state laser applications to be performed.
- With the multi-mode version of the FL laser, fiber optics of 50 to 600 μm can be used.
- The single-mode version produces exceptionally good beam quality, typically in the range of ≤ 0.02″x mrad.
- The excellent beam quality also allows the efficient use of “dynamic beam” scanner systems for high-speed positioning as well as the fast and precise application of small geometries at work pieces. This reduces cycle times and increases productivity.
- Non-productive times are reduced and the utilization of the laser is increased.
PRECITEC HP SSL Cutting Head
The HP SSL cutting head is ideal for use in flat bed systems and pipe-cutting machines with fiber-coupled lasers. Modeled on the design of the successful and reliable HP series, this head has integrated distance sensor with extremely durable stability and a monitored protective window cartridge. Pre-adjustable cartridges enable ultra-fast replacement when cutting different work piece thicknesses.
Efficient
- high cutting speeds with integrated distance sensor
- short conversion times with fast changing of focal lengths
- optimized cutting gas flow
Flexible
- cutting of different material thicknesses
- 2D cutting
- Focal length tailored to your application
- All media connections located in upper part
User Friendly & Safe
- simple and safe cartridge replacement system with TCP retention
- fast change of protective glass
- motorized focal position adjustment (optional)
- temperature monitoring of the sensor insert
- cartridge monitoring for presence
- magnetic breakaway coupling
Power Automation Controller
Power Automation CNC control with integrated inputs and outputs
- the open, browser-based human machine interface PA HMI
- the PA 8000 LW CNC
- the PA dongle which includes all needed software functions for fiber cutting
- the I/O module PAMIO which provides 4 analog in- and outputs
CAD CAM
Lantek Expert
FIBERMAK uses Lantek Expert Cut Cad/Cam Software by its own post-processor. Its many features such as automatic nesting and machining, calculation of time/cost, micro-joint, common cut etc. makes cutting easier.
Easy Programming Features
- Cutting Technology Charts according to material types and thicknesses
- Automatic nesting + processing
- Time and cost calculation
- CAD module
- Micro-joint
- Common cutting
- Film burning
- Automatic I/O
TECHNICAL SPECIFICATIONS (Click link below)
Touch Command EVO
The Newest Evolution in CNC Technology
MG is very proud to introduce the Touch Command EVO – the latest version of their popular CNC system completely designed and flawlessly integrated with MG machines through years of research and development. The control retains its easy to use interface on the surface of previous controls that our customers have enjoyed; however, underneath it there is an all new extremely powerful engine which delivers a precision of control never before found on a plate rolling machine. This is mainly achieved by the new closed loop system which constantly monitors the rotation and side roll positions.
There are some unique challenges when it comes to designing a true CNC control for a plate rolling machine. The main challenge is the difference in yield tolerances of the material being rolled.
Let’s look at A516 gr70 which is one of the most common types of steel plate used today. It has a minimum yield rating of 38,000 psi; however, it’s possible for the yield to be higher than the minimum rating, let’s say 45,000 psi for this example:
Company A is receiving material that is 38,000 psi from a supplier in the Northwest and company B is receiving material from a different supplier in the Midwest that is 45,000 psi. If these two plates are rolled on the same machine using the same settings they will roll to different diameters due to the different yields even though they are both A516 gr70 plates. There is not a CNC control available that can take these differences into account and automatically adjust for them without some operator intervention.
MG has taken the unique approach of designing a material library that can be adjusted to work specifically with the material you are receiving. This is done by making 3 test bends with your specific material and inputting the diameters that were actually achieved. Once this is done and the computer understands how your material reacts or springs back, it can accurately auto-generate programs of virtually any shape required with the material you adjusted the library for – round, square, triangle, elliptical, etc.
If you do happen to buy material that has a slightly different yield than normally you can use the powerful corrections page which gives you the ability to adjust any section of the part you are rolling independently. The transitions on parts with more than one diameter are flawless due to the all new closed loop system that was designed to check for the correct side roll position every 0.039 inches of rotation. If the side rolls starts to deviate from the correct position during a transition the rotation will speed up or slow down automatically to ensure the transition is correct. This is crucial when rolling parts with changing diameters.
There is also a completely new CAD system included which allows you to draw shapes to be rolled right on the control or if you prefer you can upload a DXF file. After your shape is loaded just choose your material and the computer will generate a program to roll your part. The number of steps in a program along with how many programs can be stored are virtually unlimited. The touch screen is easy to navigate and can be used while wearing gloves. Programs can be backed up via USB keys for easy offline storage.
The CNC Touch Command EVO is the most user friendly and accurate rolling sytem ever produced for a plate roll. Thanks to the above-described closed loop system the material waste has been virtually eliminated.
Technical Characteristics:
- Amount of saved programs is virtually unlimited
- Amount of steps per program is virtually unlimited
- Linux operating system
- New generation mother board conforms to Rohs regulations
- Integrated graphical card with accelerated 3D hardware
- Intel Celeron Mobile 1.5 GHz CPU with lower operating temperature (optimal for industrial environments)
- Memory DIMM type DDR 1 GHz
- The direct connection of the LVDS display leaves the VGA port open for connecting an external monitor
- The touch screen display conforms to Rohs regulations
- Calculation Capacity has tripled compared to previous versions
- Front panel with more input/output ports: 2 USB, 1 Serial, 1 Ethernet
When choosing a 4 roll machine with a CNC control there really is no better choice than the Touch Command EVO.
Plasma Burning Machine
Cutting with profit. Less scrap, more automation, higher performance.
Standard Features
- Solid steel construction designed for high speeds
- Fume extraction table with pneumatic switch control, exchangeable grills, dross collecting system which allows clean, safety and healthy working environment by vacuuming dust and fume which raises during plasma cutting process
- High precise positioning possibility with linear sledge system in all axis
- Synchronized drive allows a smoothly and vibration free motion
- Brushless AC servo motors ( on all axis)
- Pinion and gear rack drive system facilitates smooth and fast motion
- Up to +.004” precise positioning
- Automatic height control and automatic ignition torch system
- Torch collision protection
- Windows based CNC control unit
- Vestige plate stock management database with optional auto-nesting program which provides economy on material and saves time
- In comparison to laser cutting, plasma cutting decreases the cost of the process by 20%. With similar cutting quality, plasma is a preferable alternate to laser cutting.
- Cutting surface is close to 90 degrees and the vertical roughness tolerance is in minimum level.
- Manual
HYPERTHERM EDGE UNIT (USA)
- Graphical user interface, easy and flexible use with SOFTMOTION technology
- Windows based industrial PC
- Touch screen display
- Strong and reliable processor
- 15” LCD Monitor (touchscreen)
- Standard PC power supply
- Automatic and manual control during oxy-cutting process
- USB, CD, floppy disc input to load the shapes
- Cutting processes are can be followed from the screen
HYPERTHERM 130
- Cutting mild steel from .020” to 1.5”
- Prevents dross by cutting, so no second cutting process required
- Easy, fast and correct gas usage through optional auto gas control.
- Saves cost by high definition cutting quality.
- Depending on material no or only little dross formation
- Durable torch consumables
- Minimum gas and energy loss through high definition plasma arc technology
- Repeatable cutting quality
- Perfect cutting quality of Hy-performance on stainless steel
- Durable consumables
- Hy-performance plasma control is user friendly.
- Changing of the torch very easy and fast
- Bevel cutting possibility up to 45 degrees.
- Marking is also achievable with the same torch. With the continuously
current gauge the cutting performance could be repeated up to 1-9/16”.
HYPERTHERM Command THC
Height control
- Torch height control can be adjusted easily by arc voltage feedback control which affects the cutting quality positively.
- Collision avoidance system is designed mechanically and electronically.
- Torch height control system through microprocessor.
- All values and also errors could be found easily through the relaying indicators.
- Optional breakdown is designed in order to reduce or eliminate damage to the torch due to accidental collisions in all axis.
- System control can be reviewed or can be transferred to the CNC control.
Fabtech 2010 in Atlanta
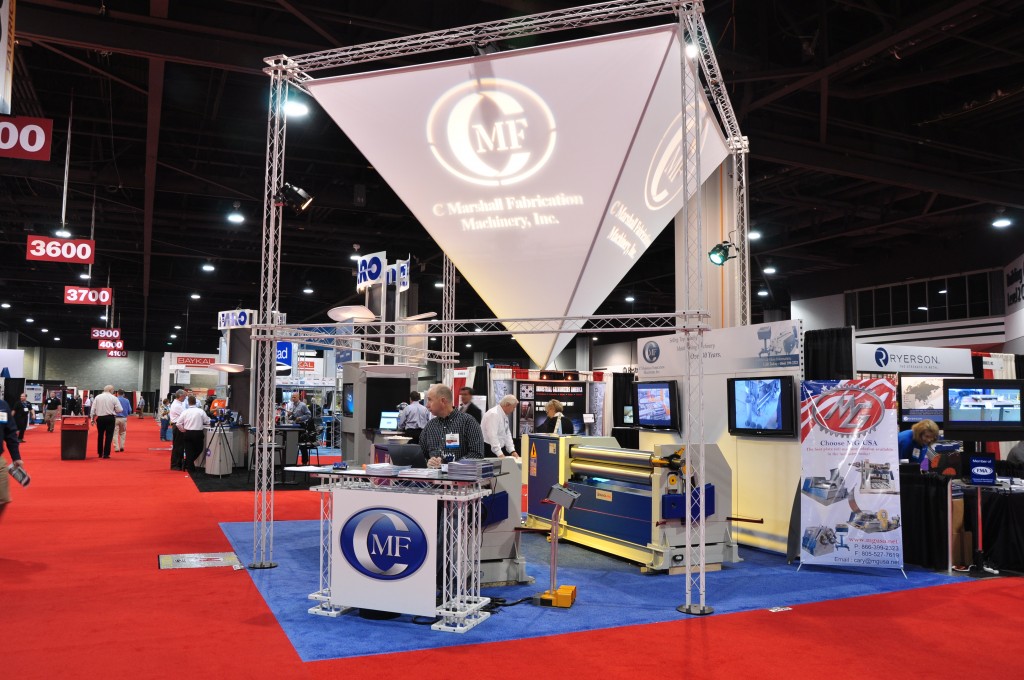
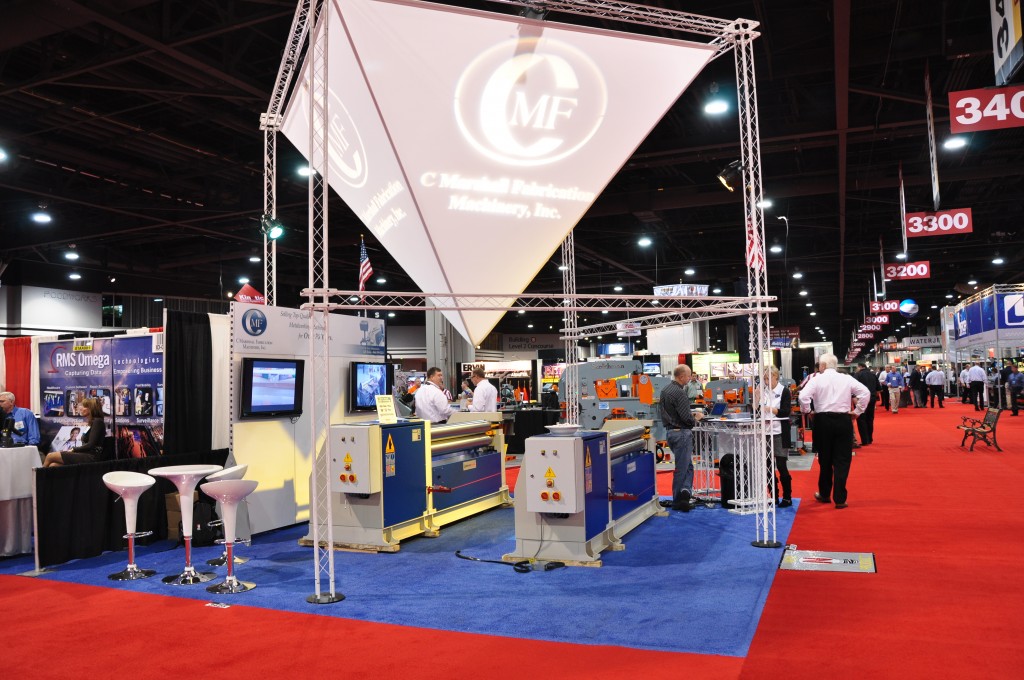
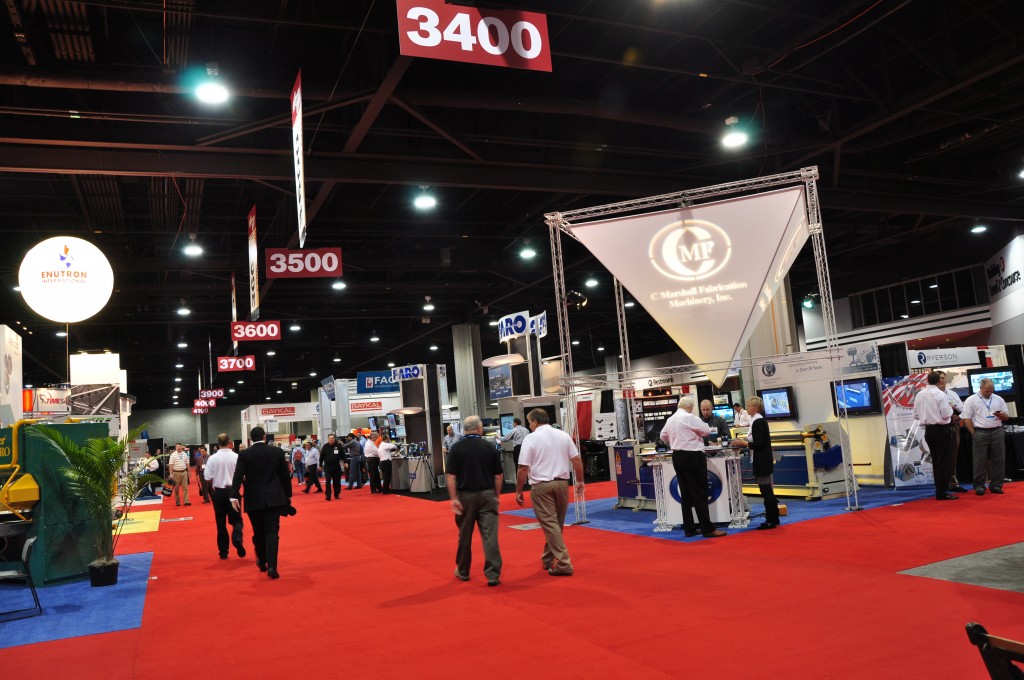
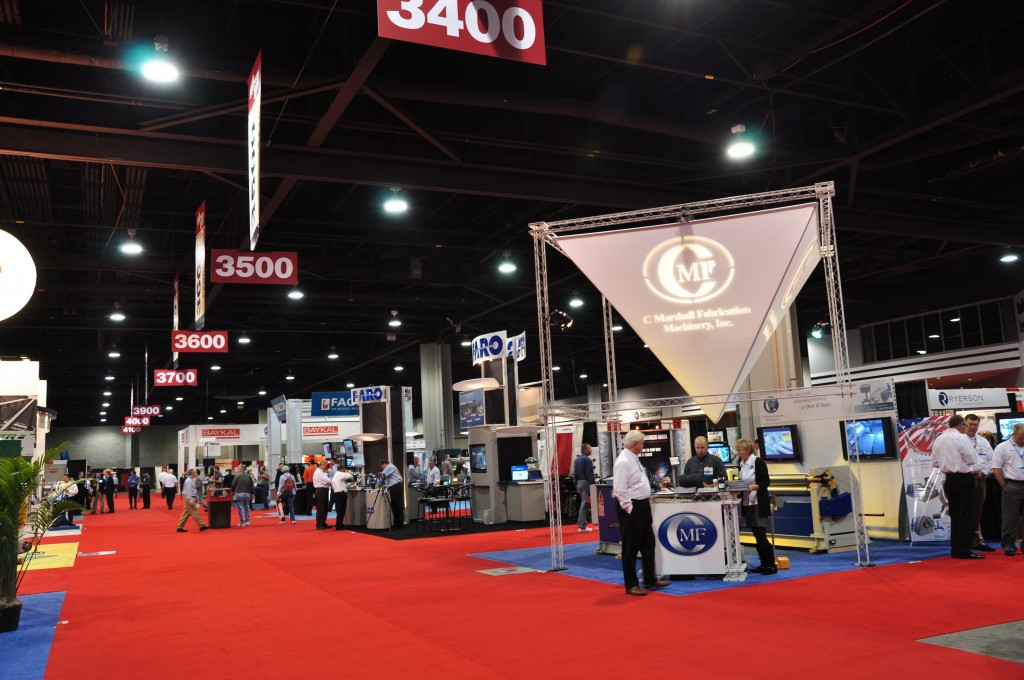
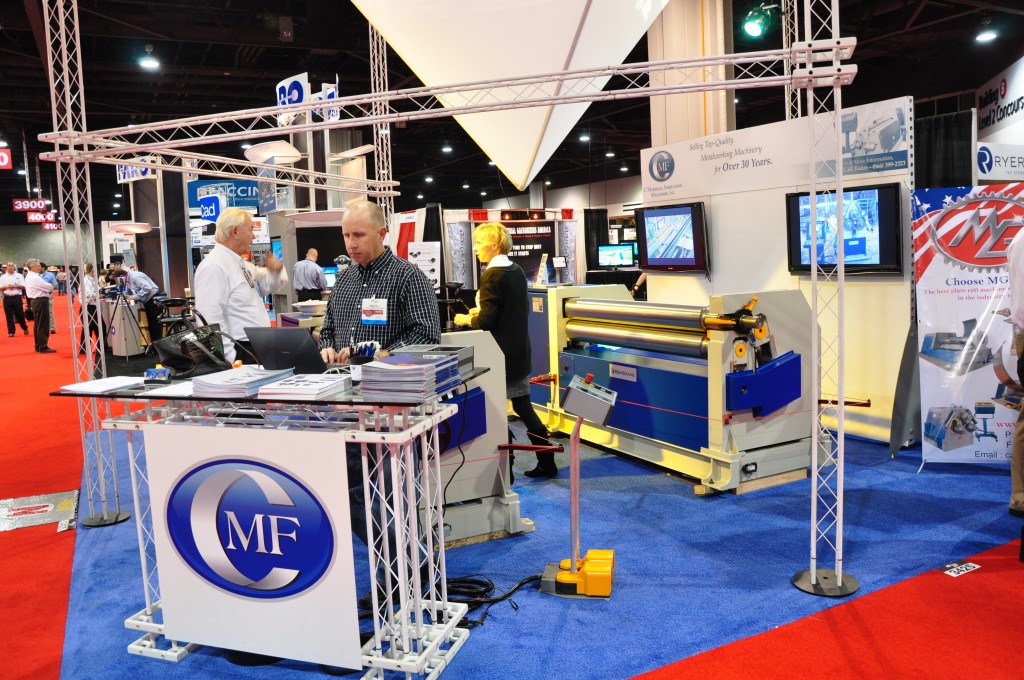
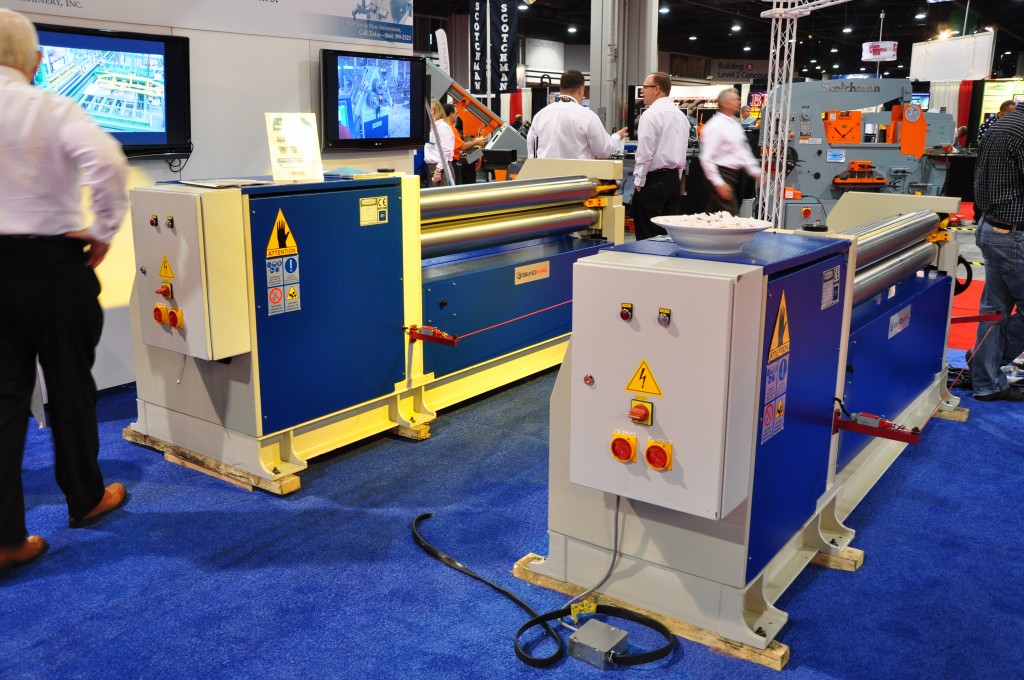
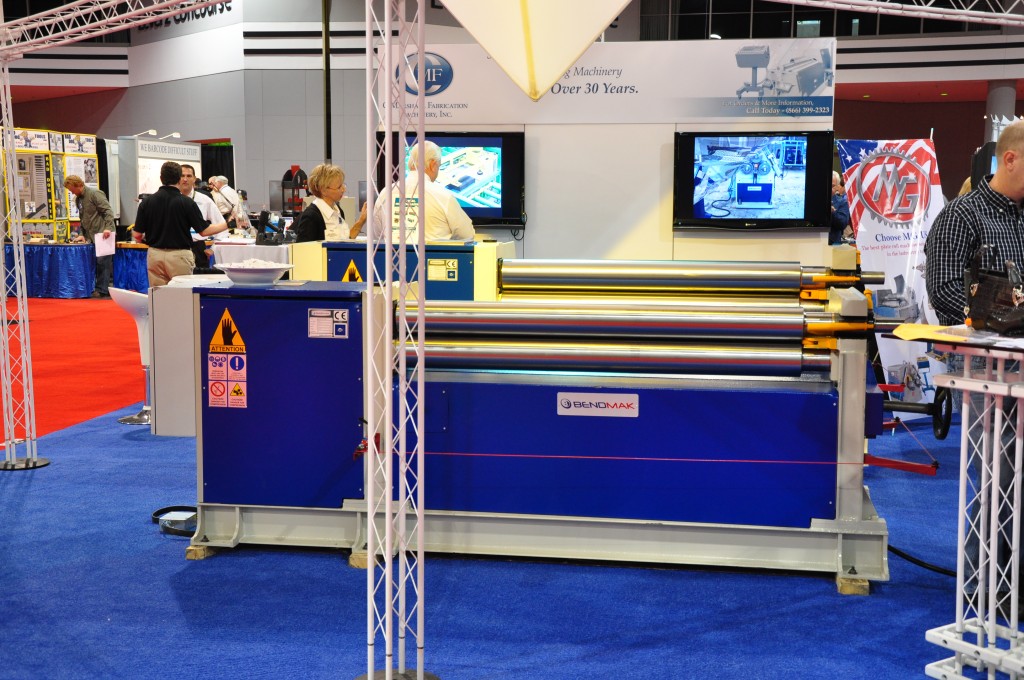
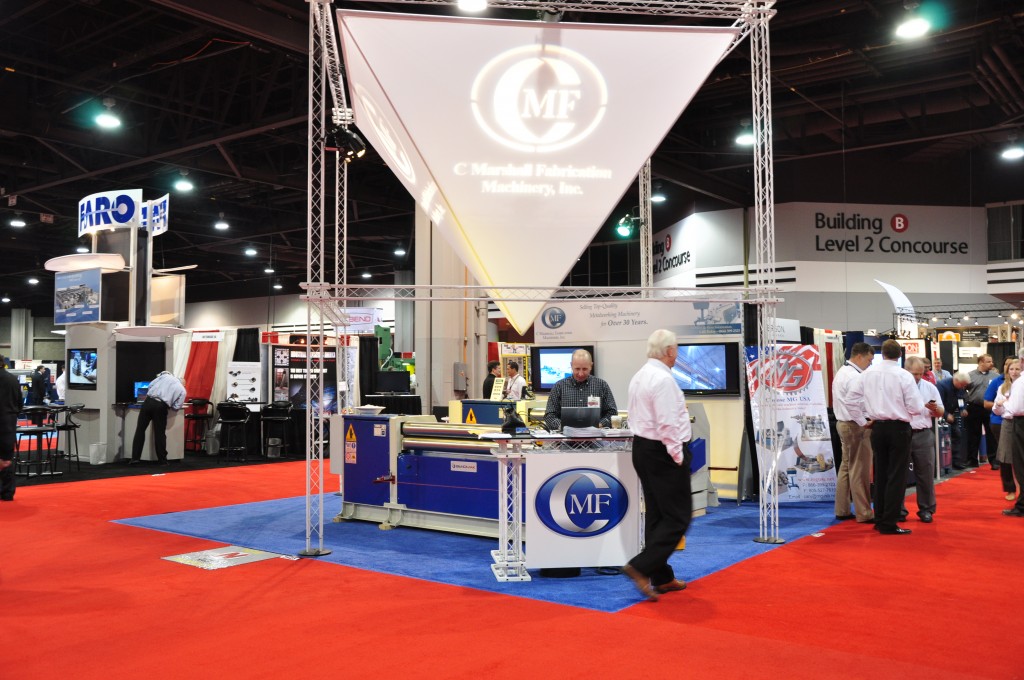
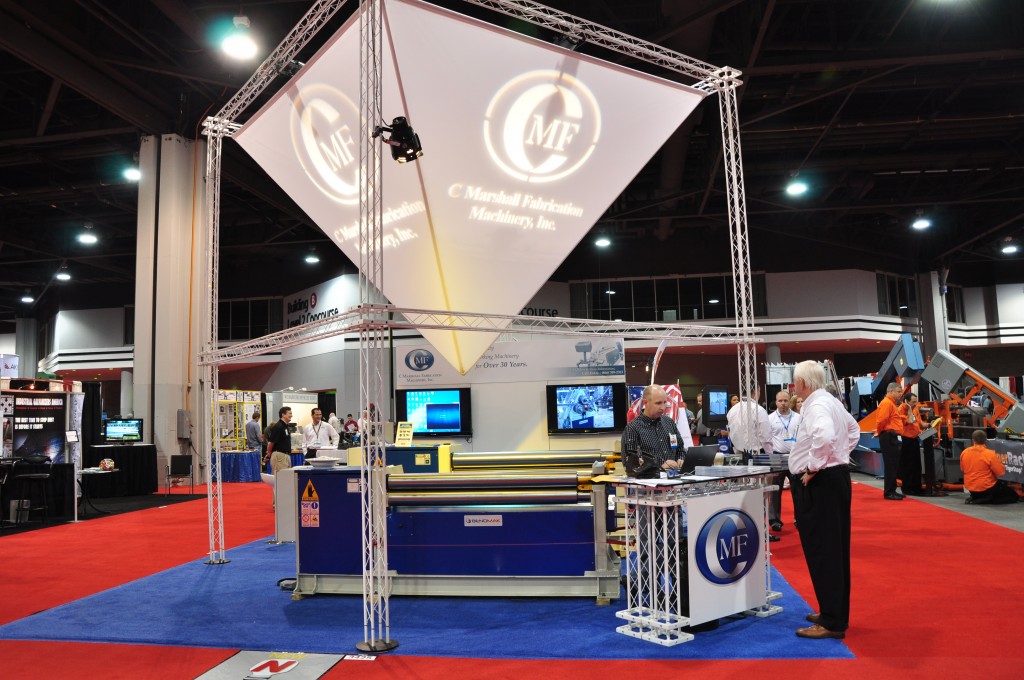
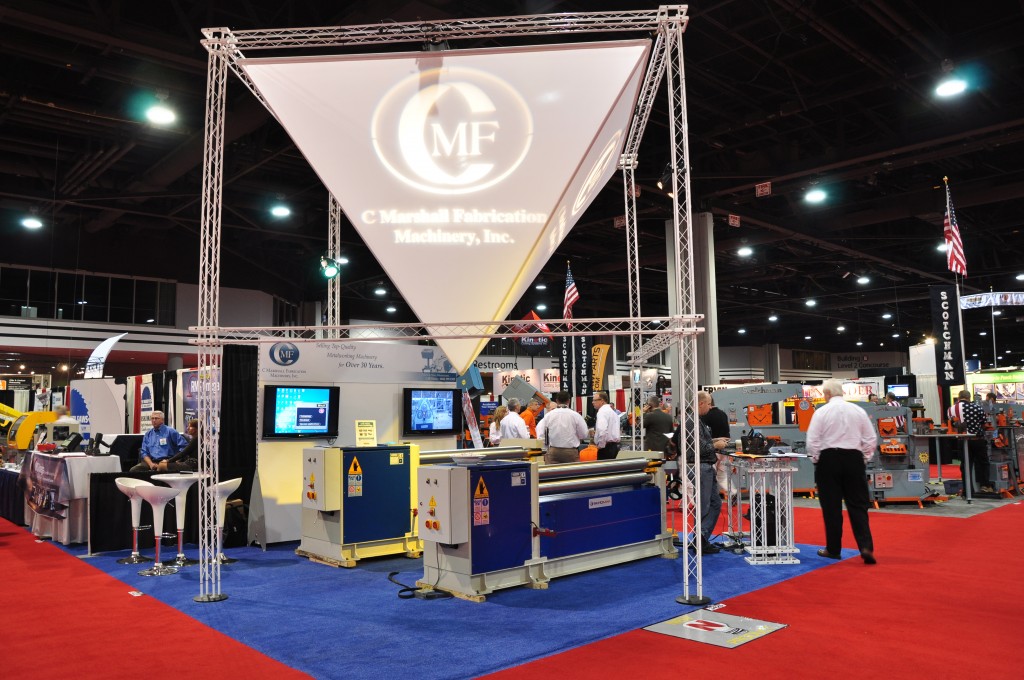
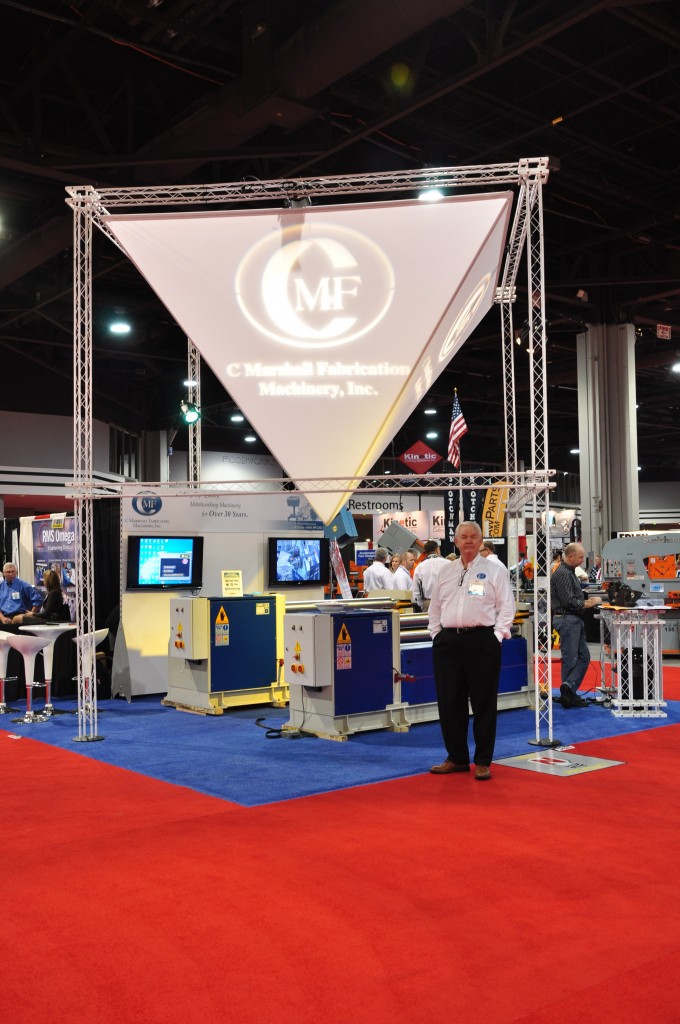
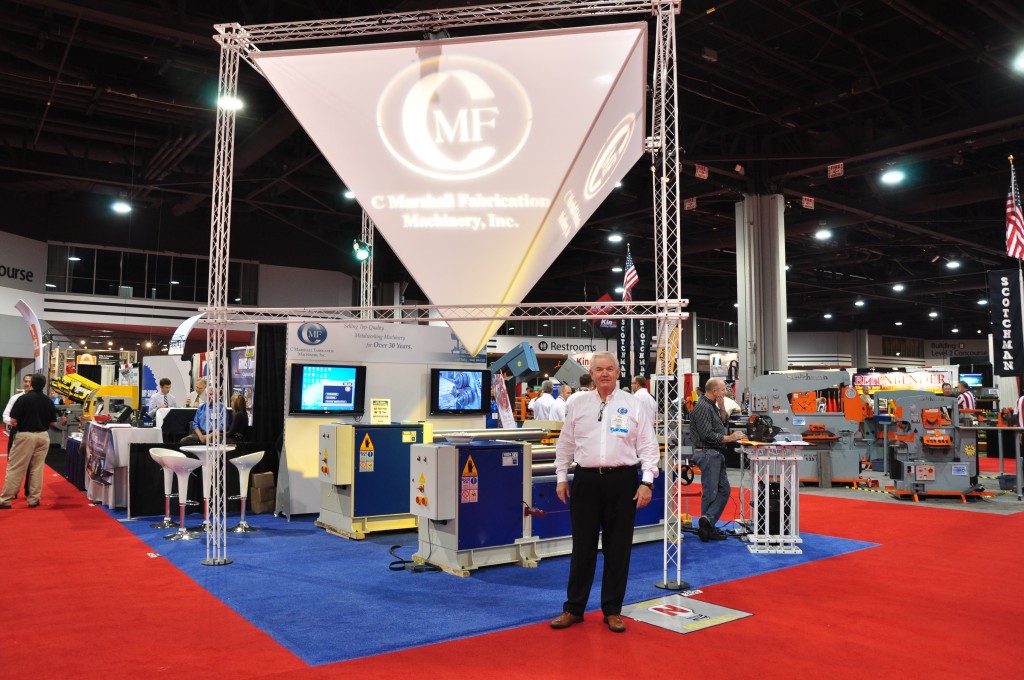
BENDMAK Hydraulic Profile Bending Machines
PRO 80
PRO 60
PRO 50
BENDMAK 2-, 3-, 4-rolls
CYL-ST 3-roll Asymmetrical Plate Bending Machine
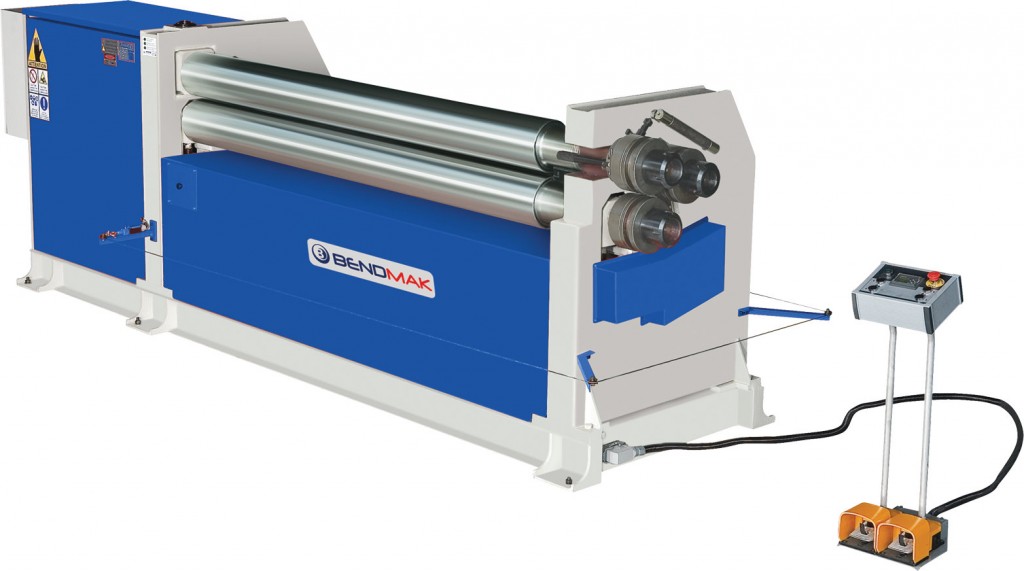
CYL 3-roll Asymmetrical Plate Bending Machine
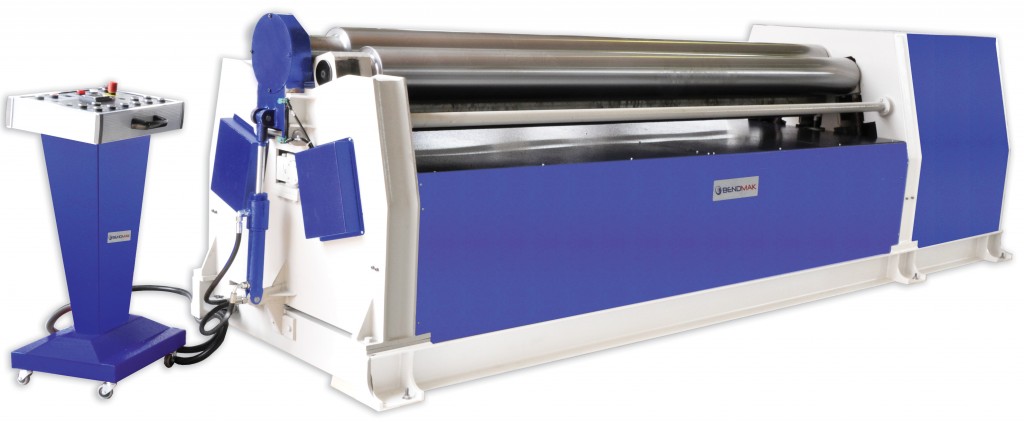
MG 32520Z pictures
When you talk about WOW factor… Here is something to marvel.
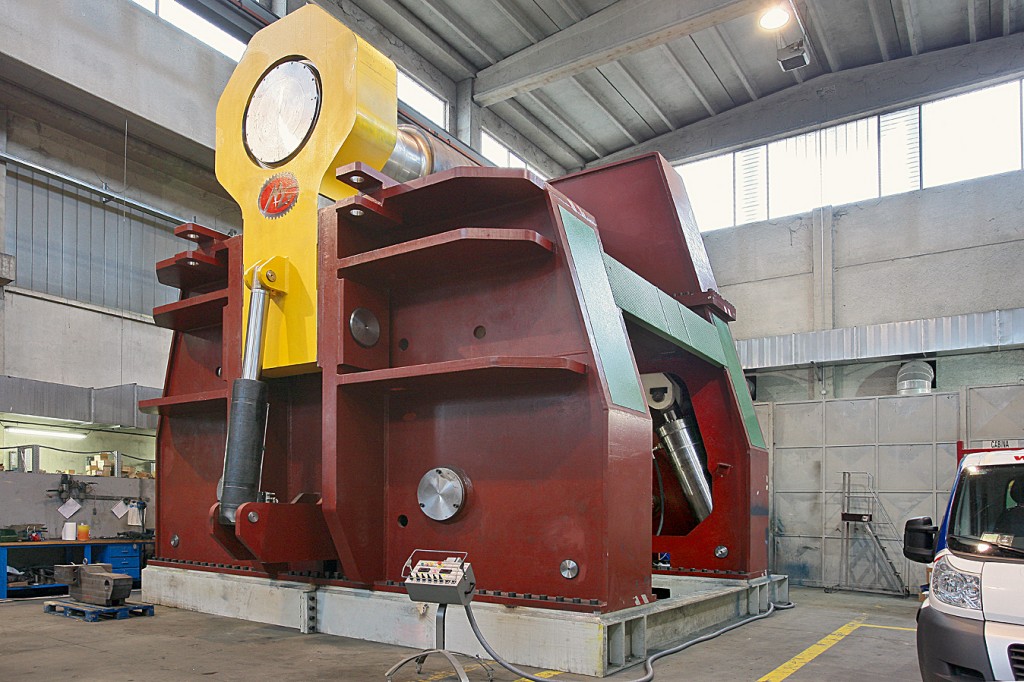
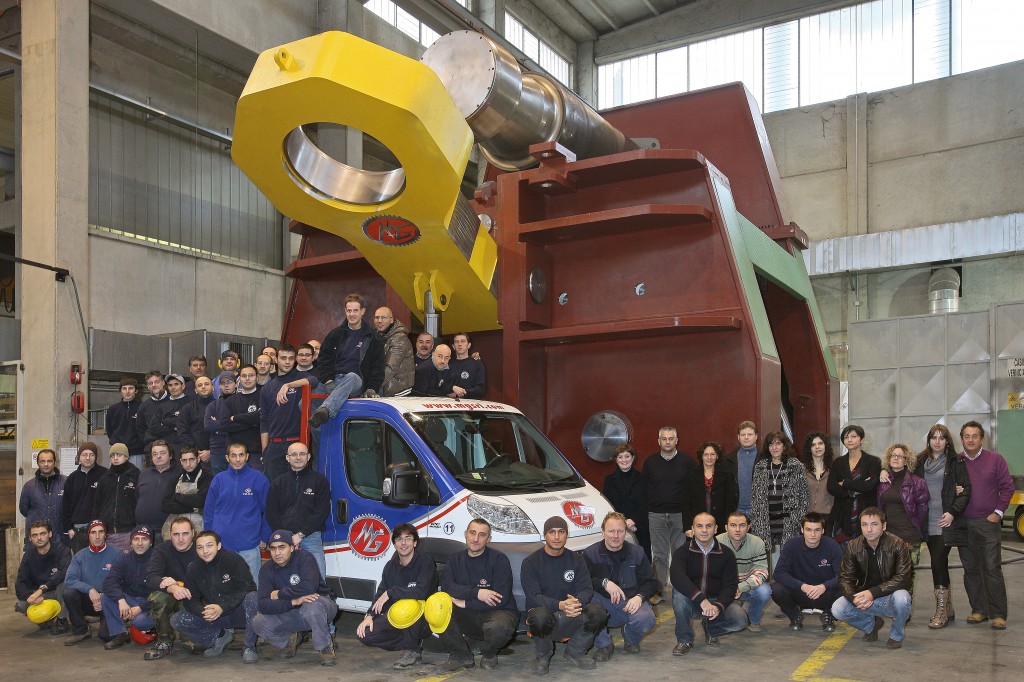
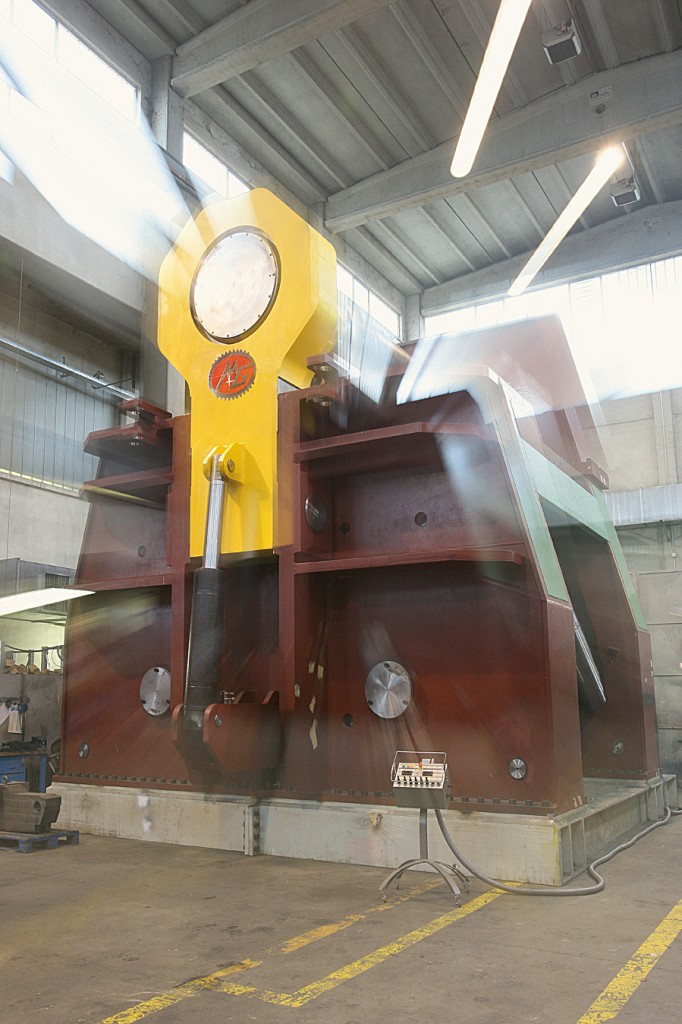
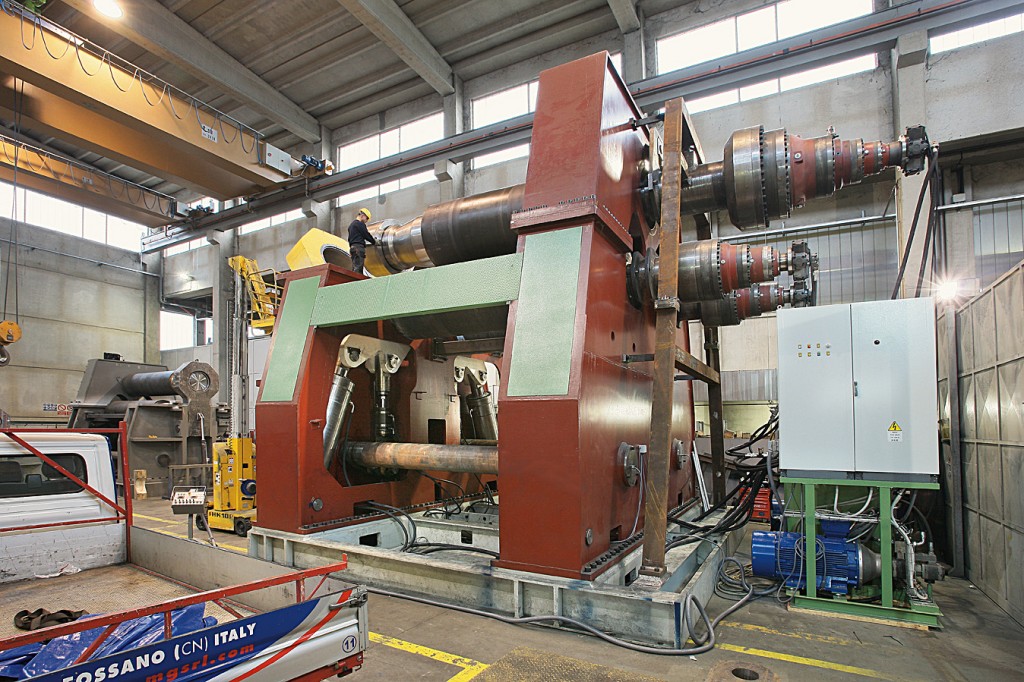
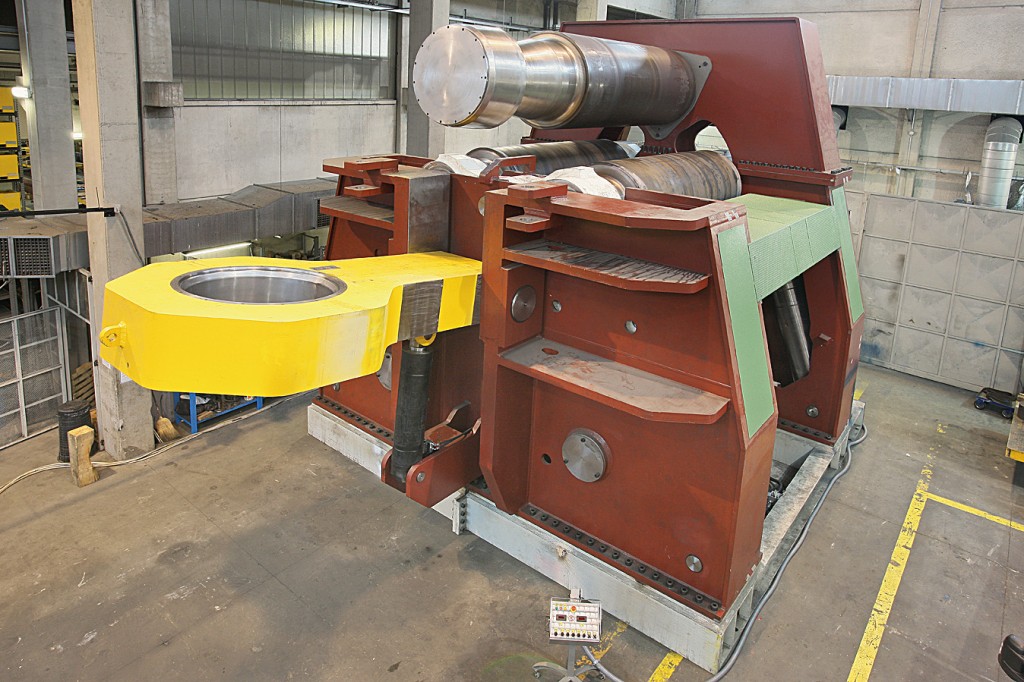
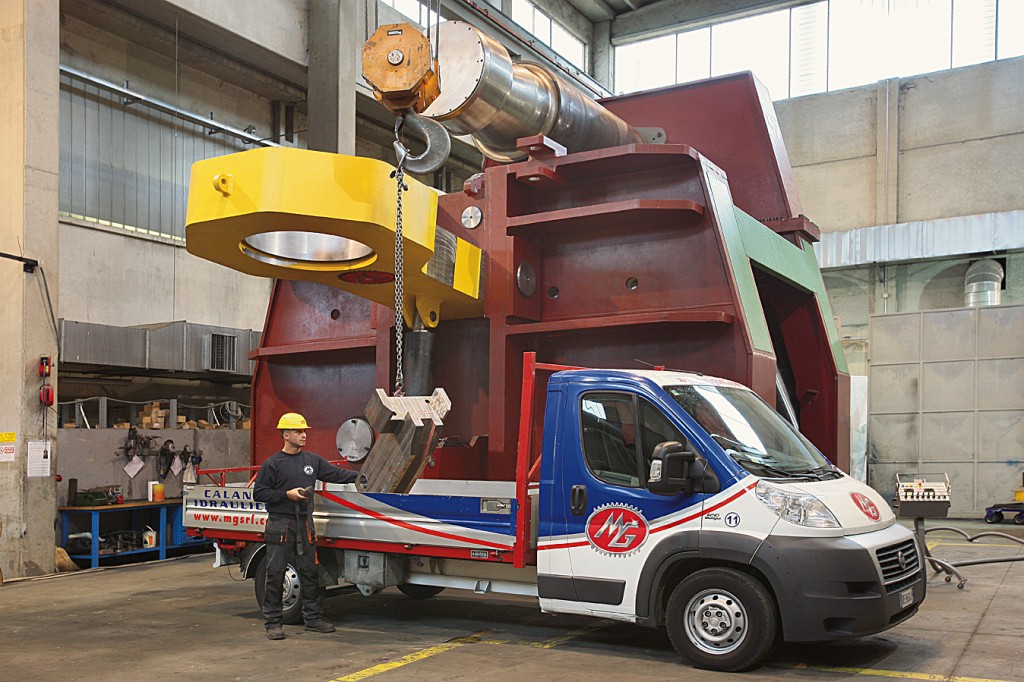
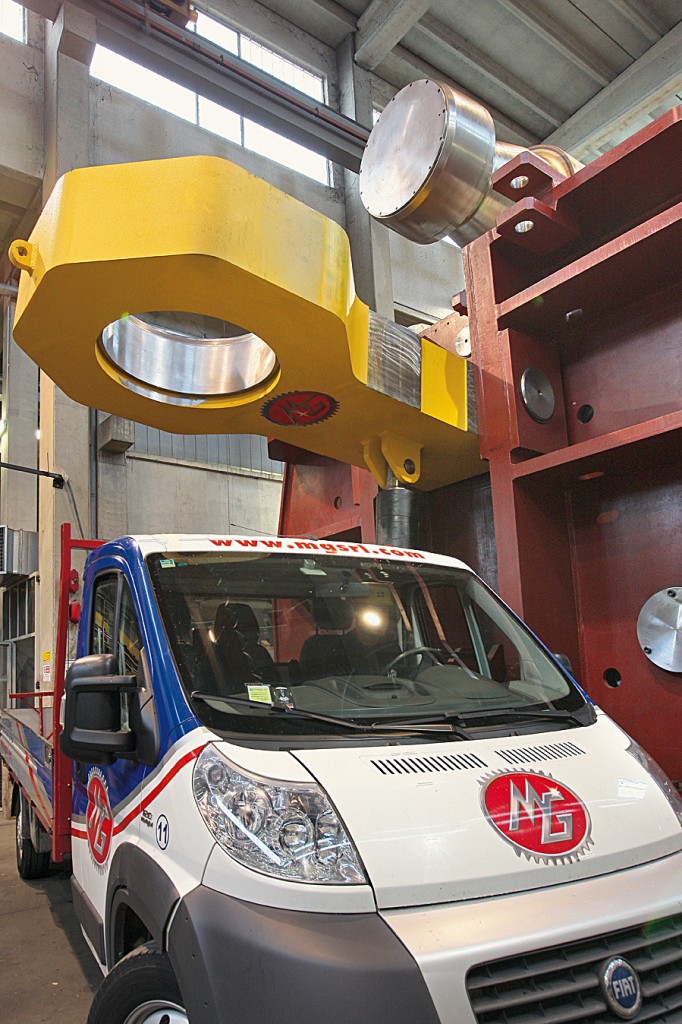
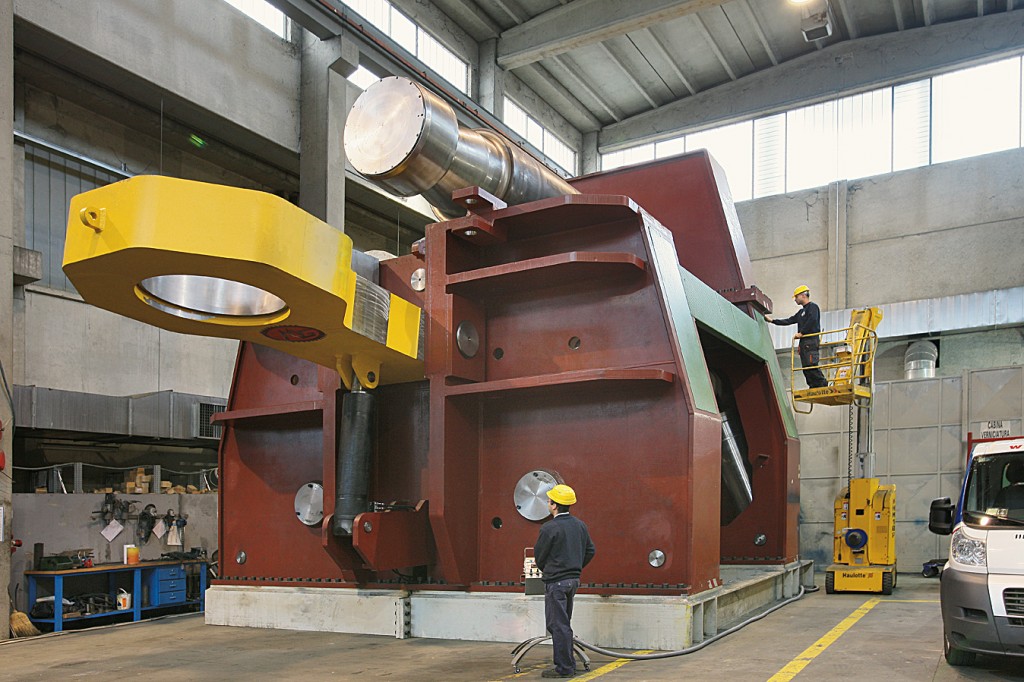
MG & G line – 3 Double Pinch Plate Bending Machine
Technology
Frames made out of welded steel and worked on CNC milling-boring machines.
Power drive: The “G-MG” has all rolls powered with hydraulic motor and planetary gear box. All rolls made out of forget steel. All movements are hydraulic. MG owns a new geometry bending system characterized by radial movements of the bending rolls and movements totally assembled on high load dynamic bearings that grand minimum friction and a smooth rolling even when the machine works at its capacity limit.
The bearings supporting the rolls are mounted in watertight compartments with grease, protected from the external dust and pollution and having permanent lubrication. The hydraulic motors of the rolls are coupled to their epicycloidal gear boxes. The gear boxes are mounted directly on the rolls without secondary transmissions; this way there is no loss of power and no need of parts maintenance.
Massive torsion bars grant the absolute rolls parallelism. These torsion bars, together with all the hydraulic device, generate a system that gives absolute precision and versatility. The MG-G Three Roll Double Pinch plate roll is the most advanced three-roll double pinch roll on the market today!
Whether you are a job shop or manufacturer, the MG Three Roll Double Pinch is the best solution. The MG Three Roll Double Pinch plate roll is the most advanced three-roll double pinch roll on the market today!
Standard Features
- Fully hydraulic heavy-duty plate bending machine
- Elimination of daily, weekly or monthly maintenance
- Lifetime parallelism
- No proprietary replacement parts
- Off-shelf parts available in most cities
Spherical Roller Bearings

Spherical roller bearings are extremely energy efficient. Eliminates bushings and the necessary running tolerance they require. A negligible loss of energy due to friction whereas bronze bushings take 25-30% of available energy to overcome inherent friction.

Lubricated for life.
Torsion Bar Parallelism


Torsion bar parallelism: unlike electronic systems or proportional valve systems, which maintain a theoretical balance, the MG Roll maintains a mechanical finite parallelism through our exclusive torsion bar system which allows the machine to be adjusted to its full conical tilt and back to parallel in only 5 seconds for the life of the machine.
Planetary Guides
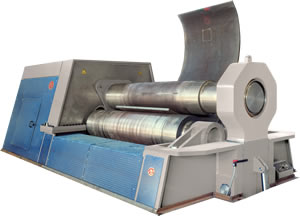
MG3110T, 10′ X 4-5/16
By using exclusive planetary guides, available on MG Rolls, we are able to keep more area of the plate under bend pressure during the rolling operation, thereby allowing the MG Rolls to roll down to 1.3 times the upper roll diameter. This allows MG Rolls to have a 16% advantage on tight diameters over our competition.
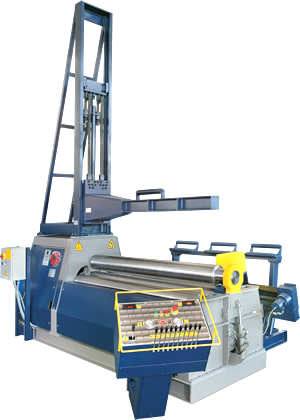
G1706P, 68″ X 1/4″
All three rolls are independently driven by planetary gear drives. This eliminates complicated transmission systems which are not energy efficient. Delivers in excess of 98% of all created energy to the roll surface. Also eliminates the need for clutches and complicated synchronization devices.
G 3-Roll Specifics
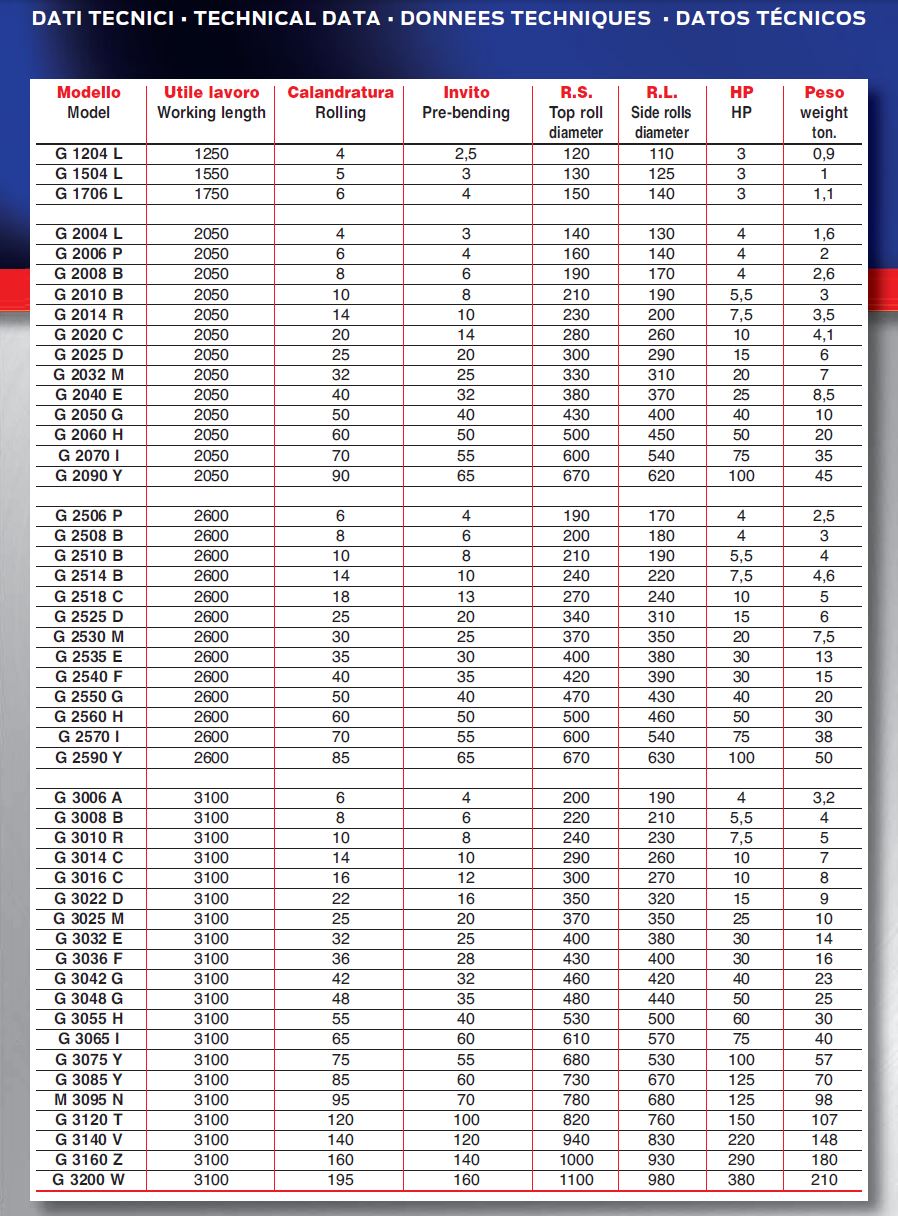
MG 3-Roll Specifications
Click Here for Brochure
Video below showing the G model
PRO 100 Hydraulic Profile Bending Machine
PRO 100 rolls are driven by hydraulic motor + planetary gearbox and gears.
- Machine body manufactured of st-52 special steel
- Built in accordance with EU norms
- Rolls and shafts are made of special steel (42CrMo4) – Induction hardened and grinded
- Side guide rolls are in one direction manual adjustable
- Vertical and horizontal working possibility
- Hydraulic and electrical protection against overloading
- Digital readout to display position of lower rolls
- Torque limit device to prevent overloading during bending
- Independent hydraulic up and down movement of the bottom rolls
- One universal set of profile roll
- Portable control panel with foot pedal in order to control material from required locations.
- Manual lubrication
- Detailed instruction manual
Optional accessories:
- Special profile rolls for bending pipe, H, I, U, etc type materials
- Special mechanical guide rolls in order to facilitate angle bending for PRO 100
- Electric motor according to required voltage and frequency
- Hydraulic guide rolls for PRO 100 model in two directions
- Digital readout for displaying the position of the hydraulic guide rolls
- Spiral bending device
- Variable speed of rotation
- NC playback and NC graphic control system
PROFILE | PRO 100 |
![]() |
2″ X 1/4″ (28″ DIA) · 3-1/2″ X 5/16″ (40″ DIA) · 4″ X 3/8″ (47″ DIA) |
2″ X 1/4′ (32″ DIA) · 3″ X 5/16″ (47″ DIA) · 4″ 3/8″ (63″ DIA) | |
4″ (47″ DIA) | |
4″ (40″ DIA) | |
4-3/4″ (47″ DIA) | |
1-9/16″ X 3/8″ (16″ DIA) · 4″ X 3/4″ (24″ DIA) · 4-3/4″ X 1″ (63″ DIA) | |
2-3/8″ X 3/8″ (16″ DIA) · 4″ X 1-9/16″ (24″ DIA) · 8″ X 1-3/8″ (40″ DIA) | |
1-3/16″ (16″ DIA) · 2″ (20″ DIA) · 2-3/8″ (40″ DIA) | |
1-9/16″ (16″ DIA) · 2-3/8″ (24″ DIA) · 2-3/4″ (32″ DIA) | |
2″ X .080″ (24″ DIA) · 4-3/4″ X .080″ (79″ DIA) · 1-9/16″ X .118″ (118″ DIA) | |
2-3/8″ X 1/8″ (16″ DIA) · 4-1/2″ X .141″ (40″ DIA) · 4-1/2″ X 3/16″ (24″ DIA) | |
1-9/16″ X 3/4″ X .080″ (20″ DIA) · 4″ X 2″ .197″ (118″ DIA) · 5-1/2″ X 1-9/16″ X .118″ (157″ DIA) | |
2″ X .098″ (20″ DIA) · 3-1/2″ X ,157″ (98″ DIA) · 4″ X 4″ X .118″ (118″ DIA) | |
3″ X 2-3/4″ (32″ DIA) · 8″ 3″ (47″ DIA) | |
3″ X 2-3/4″ (32″ DIA) · 8″ 3″ (47″ DIA) | |
3″ (24″ DIA) · 8″ (32″ DIA) | |
4-3/4″ (40″ DIA) · 4″ (47″ DIA) | |
4-3/4″ | |
POWER | 15 HP |
ROLLS | 12.4′ |
SHAFT | 3.9″ |
BENDING SPEED | 213 IPM |
WEIGHT | 4,928 LBS |
WIDTH | 48″ |
LENGTH | 57″ |
HEIGHT | 66″ |
CLICK HERE FOR VIDEO ON PRO100