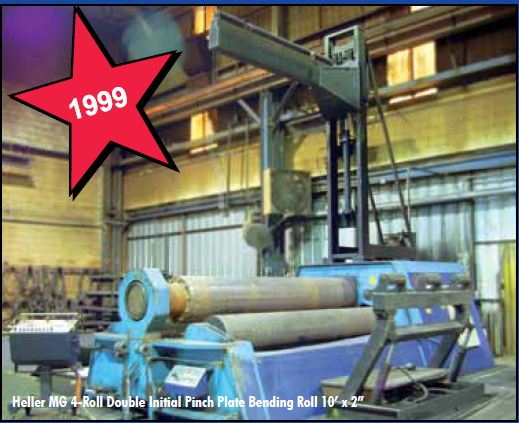
Model EH Type 350H,
SN 99047 (1999)
Plate Capacity Max 10’ x 2” Thick
Model EH Type 350H,
SN 99047 (1999)
Plate Capacity Max 10’ x 2” Thick
The ISM Manufacturing Purchasing Managers Index was broadly covered in the media, which most sources mentioning manufacturing’s key role in helping the US regain its economic footing. It was also noted that April’s expansion marked a slight decline from March, due in part to higher input costs, but that overall the results, and the outlook for the sector, are very good. The impact of a weak dollar was also noted.
The AP (5/3) reports, “The nation’s manufacturing sector has expanded this year at the fastest pace in a quarter-century, boosted by a weak dollar that has made US goods cheap overseas.” The strong manufacturing sector “could help the economy rebound after experiencing weak growth in the first three months of this year,” although other industries such as construction are still struggling, and raw materials prices remain a concern. “The Institute for Supply Management said Monday that manufacturing activity expanded in April for the 21st straight month.” Although the reading of 60.4 represents a decline from 61.2 in March, it still indicates manufacturing growth..
Bloomberg News (5/3, Willis) reports “manufacturing expanded faster than forecast in April, driven by gains in exports and inventories that are keeping the industry at the forefront of the US economic expansion.” And these same factors, “demand from emerging economies like China” and “the need to replenish stockpiles and investment in new equipment, may keep benefitting manufacturers.” Bloomberg notes that “another report showed construction spending rose more than forecast in March as companies put up factories and power plants, while home improvement outlays also rebounded.”
New York Times /Reuters (5/3, B8) reports that, according to the Commerce Department report on construction, March spending was up 1.4 percent, an entire point higher than analysts had predicted on average. However, Reuters noted, the sector remained anemic overall, having a long way to go before it can offset the declines it saw last year.
AFP (5/3) characterizes the manufacturing news in opposite terms, noting the expansion but highlighting the slowing pace of “growth in new orders, production, employment and supplier deliveries.” Norbert Ore, head of the ISM’s manufacturing committee, is quoted as saying, “While the manufacturing sector is definitely performing above most expectations so far in 2011, manufacturers are experiencing significant cost pressures from commodities and other inputs.” Daniel J. Meckstroth, Chief Economist for the Manufacturers Alliance/MAPI, however, said manufacturing was “booming.” He added, “It is clear from today’s report that the few things holding back domestic manufacturers are skyrocketing commodity prices, selective commodity shortages, sluggish residential construction and declining non-residential construction.”
Under the headline “Materials Costs Hit Factories’ Activity,” the Wall Street Journal (5/3, Murray, Hagerty, Subscription Publication) notes the same factors as AFP as impediments to growth, but adds that manufacturing continued to expand regardless, albeit at a slightly slower pace. Exports are playing a major role in many cases, such as Caterpillar, which recently reported that it was having difficulty meeting demand for some of its earthmoving equipment. That demand originates in developing economies in Asia and Latin America.
The Financial Times (5/3, Bond, Subscription Publication) notes that, of the 18 industries tracked by the ISM, only one showed signs of contracting – furniture and furniture-related products. The other 17 industries all showed expansion to different degrees.
The Chicago Tribune (5/3) reports, “The pace of expansion in US manufacturing slowed in April for a second straight month but was brisker than expected, data showed on Monday, a sign the sector was holding up despite slower national growth.” Kurt Karl, chief US economist at Swiss Re, said: “With what is happening in the world at this point, you would expect (manufacturing numbers) to be down.” He added, “We’ve had (higher) oil prices, we have had hits to Japan, we have had hits domestically from production and supply constraints from the Japanese disruptions and we are still over 60 on the manufacturing (index). So it is a very good report.” The Tribune also notes the Commerce Department report, and calls the increase in construction spending “encouraging.” CBC News (5/3) and Marketwatch (5/3 Bartash) also report the story.
From SME Daily Executive Briefing 5/3/2011
Once again this week, I threw myself wholeheartedly into a Google search for the largest metal object in the world, if only because I know that my scores of avid followers on this blog have all been holding their breath since I brought this subject up in last week’s blog entry. And once again this week, I got completely sidetracked. You would have too, after scanning the Google results for “large metal object”.
Just so you can have a better understanding of what came up on this search, here are a few samples:
“A large metal object drifts slowly through space…”
“An unusually high-velocity large metal object concealed in the nasal septum.”
“Large metal object found located under sea”
“Trapped inside a large metal object flying for ten hours.”
“Large metal object falls from sky in Roosevelt”
“A college student was killed in a freak accident when, according to police, a large metal object fell on him Friday”
“I have a large metal object caked in cement. “
“Have you ever wanted your very own custom-made metal object?
I admit that an unusually high-velocity large metal object concealed in the nasal septum REALLY grabbed my interest for a while, but I just couldn’t figure out how to turn that into something relevant to C Marshall and my thousands of devoted readers on this site. So on went my search, with many detours, until my search fingers were stopped dead in their tracks by the following Google result:
“Magnetic Boy, 7, attracts electronic and metal objects”
The first thing I did, of course, was click on the above and read the information about this Magnetic Boy. It came from a legitimate source and there was no air of “hoaxiness” in it.
Then I watched the video. You can watch it for yourself right here: Magnetic Boy
Folks, this kid is for real. He’s magnetic. Metal is attracted to him and sticks to him. In the video, he’s got forks and knives and the TV remote stuck all over his chest. No one else in his family is magnetic and of course there’s no good explanation for this, but there is no denying that this boy is a human magnet. He’s not allowed near the computer because he makes it go weird. I’m sure he’ll have a lot of trouble with credit cards, cell phones and electronic keys too. For some reason he can even get china plates to stick to him. However, because this is a blog about metal and metal machinery, we don’t really care about the china plates, do we?
Imagine having a magnetic boy of your own. You wouldn’t need a metal detector anymore: you could take him to the beach to find buried treasure, coins and jewelry. Once a huge chest of gold coins gets stuck to his chest, you can cash out and buy yourself a sturdy boat. Now you’re really in business: load up the kid on your boat and head for the high seas. Sooner than later, giant shipwrecks, plane wrecks and other metal objects of all kinds will get sucked to the ocean’s surface and you can help yourself to what you want and sell the rest as scrap metal. Now that you’re the scrap metal king of the world, you can take him to Ghana or Venezuela or Mexico or Nevada to find gold and other underground precious metals. You’ll already have the cash from your scrap metal operation to fund your mining business.
Now you can retire in style and pretty much do what you want. You might feel inclined to contribute to the betterment of humanity by renting out your kid to the military to ferret out terrorist organizations by finding their weapons stashes. Once that mission has been accomplished, you can rejoice that you have now created world peace.
I wasn’t able to find any more recent updates on the Magnetic Boy. Is it possible that he already went underground and had something to do with finding bin Laden’s location?
I wouldn’t rule it out.
-Anja Wulf
I’ve been curious for some time to find out what the largest metal object in the world is. By “largest metal object in the world”, I mean an object that is formed out of solid metal and is one contiguous piece of homogeneous metal. In other words, search results that yielded things like “largest metal sculpture in the world” don’t count, in my opinion. Additionally, I was looking for something that served an actual purpose, not just something to look at.
I still haven’t found a contemporary answer to this question. But that’s because I got sidetracked. Without question, I have learned what the largest piece of cast metal in the world was – back in 1893.
The USA was in a severe depression, marked by the collapse of railroad overbuilding and shaky railroad financing which set off a series of bank failures. Meanwhile, plans were underway to celebrate the 400 year anniversary of Columbus’ discovery of America, in Chicago, and in typical American style, a minor glitch such as the worst depression to date in the US wasn’t going to get in its way. The name of the game called upon civil engineers to build something truly unique that would demonstrate the possibilities of modern engineering in America, similar to what the Eiffel Tower had done for the French.
One man in the audience took to the challenge right away. His name was George Washington Gale Ferris, and his specialty was building steel bridges. Soon to become known as somewhat of a freak (“the Man with the Wheels in his Head”), he had a plan to build a giant wheel that people could sit in, just for fun. And sure enough, in spite of the fact that his idea had no practical value whatsoever (besides making history in the Columbus Fair) and that it required a lot of money, Ferris’ enthusiasm was catching, and he raised the money to make his plan into a reality.
On its completion, Ferris’ Wheel weighed 2,079,884 pounds. The axle alone, forged by Bethlehem Iron Company (later to become Bethlehem Steel), weighed 89,320 pounds. Powered by 2 steam engines, it could carry up to 2160 passengers at one time. It was a colossus; and without question, it was the largest piece of cast metal in the world. Most notably, although it can be argued that it was built for fame and glory, its actual purpose was pure fun.
The Ferris Wheel became a huge overnight sensation, eventually spawning plenty of stories and legends about people falling off the Wheel, etc. Although untrue, these stories took a toll on the Wheel’s popularity, and soon only few people could be seen riding on the Wheel. This wondrous feat of engineering, which had required over $400,000 to build in 1893, was sold at auction in 1906 for $1800. A decision was made to take it down, and on May 11, 1906, the Ferris Wheel was blown to bits by a “monster charge of dynamite”.
George Ferris, the inventor of the Ferris Wheel, didn’t do much better. Similar to many contemporary Hollywood overnight celebrities, he became severely depressed by the looming threat of bankruptcy and his own loss of fame. He died of typhoid fever on November 22, 1896. Saddest of all, his ashes remained at a Pittsburgh crematorium for over a year, waiting for someone to take possession of them. By then, it could be said that the party was definitely over. Nevertheless, no one can take away the fact that Mr. Ferris was on of those rare birds who was crazy and brilliant enough to able to take those wheels out of his head and create something that brought a sense of joy and wonder to millions of people.
-Anja Wulf
In the wake of financial turmoil, manufacturing takes a more central role in the economic growth potential of the United States.
BOSTON/NEW YORK (Reuters) – A pair of top U.S. manufacturers beat Wall Street’s profit expectations, as a recovering global economy drives demand for products ranging from air conditioners to truck transmissions.
United Technologies Corp and Eaton Corp also raised their full-year earnings forecasts, saying that they were becoming more confident in the economy’s direction.
Textron Inc, the world’s biggest maker of corporate jets, missed analysts’ expectations on weakness at its Cessna aircraft unit, but held its full-year forecast steady.
“The rest of the year is going to be very positive,” said Oliver Pursche, president of Gary Goldberg Financial Services in Suffern, New York, which holds United Tech and Textron shares.
The first-quarter results show that strong demand from China, India and other emerging markets had offset the disruptions to supplies of some electronic components after Japan’s March 11 tsunami and ensuing nuclear crisis, Pursche said.
The U.S. manufacturing sector, which accounts for about 11 percent of the economy, has expanded for 20 consecutive months, outpacing other sectors, according to data from the Institute for Supply Management (ISM).
Activity in manufacturing grew at its fastest pace in nearly seven years in February this year, before slowing slightly in March, ISM data showed.
United Tech posted sales growth across its six divisions, whose products range from Otis elevators to Black Hawk military helicopters, and said it now sees strong global demand.
The world’s biggest maker of air conditioners and elevators earned $1.01 billion, or $1.11 per share, with strong demand for Carrier air conditioners. Analysts had forecast a profit of $1.07 per share, according to Thomson Reuters I/B/E/S.
The company raised its full-year profit forecast to a range of $5.25 per share to $5.40 per share, representing growth of 11 percent to 14 percent and marking the second increase since United Tech first issued its outlook.
When the Hartford, Connecticut-based company laid out its initial 2011 profit forecast in December, it had warned investors that U.S. and European economies looked “sluggish” and that a drop in the value of the euro versus the dollar could drag down earnings.
“The risks that we saw earlier in the year just don’t seem to be materializing,” United Tech Chief Financial Officer Greg Hayes said in an interview.
United Tech shares were up 4.1 percent to $85.74 in afternoon trading, after earlier reaching a lifetime high.
HIGH EXPECTATIONS
Industrials have outperformed the broader market over the past year, with the Standard & Poor’s capital goods index up 13 percent, while the full S&P 500 is up 9.5 percent. That rise has raised investors’ expectations heading into earnings season.
“They have to beat strong,” said analyst Brian Langenberg of Langenberg & Co in Chicago. “They have to surprise.”
Eaton, which makes truck transmissions, and hydraulic and electrical systems, earned 84 cents a share, 4 cents ahead of analyst estimates, and raised its 2011 forecast for the second time this year.
Energy and mining investment is lifting electrical sales. Hydraulics markets are being helped by demand for farm equipment, amid high food prices, and for construction machinery used in emerging markets, said Eaton Chief Executive Sandy Cutler, who also cited a recovery in truck production.
“Now that the economy is coming back, freight companies are having more success pushing prices through,” Cutler said in an interview. “They’re becoming more profitable.”
Eaton shares rose 1.3 percent to $53.34. Textron fell 2.2 percent to $25.09.
The three companies kick off a wave of earnings reports from blue-chip U.S. manufacturers. Honeywell International Inc plans to report after Wednesday’s market close and General Electric Co is due on Thursday. 3M Co and Caterpillar Inc report next week.
The sector faces a few major risks this year, including rising energy prices and the aftermath of Japan’s nuclear crisis, which threatens to curtail supplies of electronic components.
Textron, which also makes industrial components used by auto-parts makers, said it expects second-quarter sales to be hurt by lower demand from Japanese customers, but said production slowdowns will be substantially made up later in the year.
Textron’s first-quarter earnings of 10 cents per share missed Wall Street’s 17-cent forecast, reflecting still-lackluster demand for its Cessna corporate jets.
United Technologies, meanwhile, could face short supplies of key components including flash memory chips used in air conditioner controllers.
“Right now we have adequate supply; it’s just a question of making sure that we continue to have access to that,” CFO Hayes said. “We don’t see any material impact, but I think you’ll see bits and drabs of this over the course of the year.”
Scott Malone and Nick Zieminski Reuters
12:19 p.m. CDT, April 20, 2011
A guillotine shear is a machine that can shear or cut various materials with a guillotine design. The word “guillotine” is associated with a blade that drops along a vertical track. This type of machine was primarily used in familiar history as a method of execution, particularly in the French Revolution, but the modern guillotine shear cutter is a tool used to form and shape products for a market.
The principles of the guillotine shear were incorporated into the design of metal shears and have been the primary design for all of these years. Some of the shortcomings of a guillotine shear are that it must run in gibs and ways and therefore need a certain amount of clearance which has a direct effect on the thinnest sheet than can be cut (see figure 1).
Also, the ram moves down with approximately 1 degree of backward motion. This allows the cut sheet to clear the back gauge and drop, although sometimes even this is not enough and the cut part is wedged between the lower blade and the back gauge.
When a guillotine shear has a throat it must be heavily re-enforced to avoid the deflection that would normally result from a deep throat. The apron of the upper ram is heavily gusseted to keep the blades parallel to the bottom blades. This system has worked well for hundreds of years however times change and new engineering becomes available.
On a swing beam shear the ram moves on bearings so there is no play what so ever. This allows the swing beam shear to be able to cut paper as long as the blades are sharp. The ram moves from a fulcrum point in the rear of the side frames giving the shear a massive amount of plate between it and the cutting point (see figure 2). This means almost no detectable deflection.
The back gauge is attached to the bottom of the cutting column and moves up as the blade goes down. This means there will never be a possibility for the material to become stuck between the blade and the back gauge.
Rather than gussets on the apron a swing beam shear wraps the entire ram as one solid gusset making it much stronger than a similarly gusseted ram. It can have a deep throat with no possibility of deflection and can cut even the thickest piece of metal with a very low rake angle.
In my opinion the swing beam shear reviewed the short comings of the guillotine shear and fixed them; however, it is important to remember that before making a decision on purchasing any kind of a shearing machine factors such as the type of shear, required capacity, productivity options, and safety should be carefully evaluated.
One important consideration used in deciding what shear is the right one for any job is the capacity required to perform the job. Most of the shears on the market today list capacities for mild steel and stainless steel. It is advised to compare a fabricator’s requirements to those of the actual machine.
Some shear capacities are rated on mild steel, which may have 60,000 pounds per square inch (PSI) tensile strength, while others are rated for A-36 steel or 80,000 PSI tensile strength. Capacities for stainless steel are almost always less than those for mild or A-36 steel. Surprisingly enough certain grades of aluminum require as much power to shear steel does. As always, when making a decision on any kind of metalworking machinery purchase, it is important to work with a reputable and knowledgeable company that can answer all the questions regarding the performance and capacity for the machine.
From the desk of Cary Marshall
The AP (4/19) reports, “A survey from the National Association for Business Economics finds that economists are hopeful that the broader economy is substantially improving, with rising employment reported for the fifth quarter in a row. … The outlook for employment rose slightly, reaching a 12-year high,” and “nearly all of the 72 economists surveyed, about 94%, now expect the economy to grow at least 2% in 2011.”
From SME Daily Executive Briefing 4/19/2011
I’ve recently been spending a disproportionate amount of my time working on a boat. By boat, I mean a 39-ft sail boat (or cruiser, if you prefer) that we are planning to sail to the Caribbean in a few weeks. Anyone who’s owned or worked with boats will tell you that the amount of work that goes into the maintenance and upkeep of one cannot possibly be exaggerated. Re-sanding and re-varnishing the entire interior is just the icing on the cake. The electrical needs rewiring in places, the plumbing needs an overhaul, the hull needs to be scraped and repainted, the windows need to be painted and installed, and the list just keeps going on from there. In fact, it’s kind of depressing just writing about it, considering that our plan is to leave at the end of the month.
So in order to cheer myself up a bit, I decided to do a little online shopping for mega yachts. I figure if it’s this much work to maintain and prep a 39 foot boat, mega yacht owners must be offering a lot of money just to unload their boats to some poor sucker like me.
I found one that I thought was kind of cute. In case you think this has nothing to do with metal fabrication machinery, think again. This ship’s hull is made entirely of steel. It has 8 decks and platforms. Aluminum alloys are used for the manufacturing process, which are formed of seven modules which in their turn were assembled out of several different sections.
The overall length of the boat is 158 meters. For those of you who don’t know miles from meters, an average city block is about 160 meters. The upper deck also comes fully equipped with a dock hangar providing landing sites for 2 helicopters, as well as 2 locations for refueling them. So yes, that’s a lot of metal right there.
Described as a “jewel of design”, the yacht also features a huge hall with 3-story high columns, a multiple dome arched ceiling, balconies and numerous luxurious staircases, a “winter garden” described as a “real paradise corner” featuring multiple swimming pools, waterfalls, trees and lanais, and a pier for pleasure boats – sort of an island within the boat.
The central part of the yacht is built in the image of an altar and features a Throne Hall, statues of 7 major saints, golden balls which are supposed to reflect the Glory of God, golden halos, and fresco paintings attesting to the Life and Acts of God and the Saints. The main statue is a statue of God with a golden face, which “can easily be rotated around its axis, staying always to face the congregation”.
According to its own listing, “the whole appearance of the yacht is subordinated to one central message: Glory and Grandeur of show-power-Simplicity, availability and proximity to us – our Lord”.
Personally, I don’t have a clue what this is supposed to mean, but by now I’m starting to form a vague idea that the maintenance of this boat might be a little more than I could comfortably handle. I’m also thinking that the cost of filling up her tank would be more than what I earn in an entire year.
Which, of course, makes me even more confident that the owners must be willing to pay a lot of money to someone who’d volunteer for the responsibility of being saddled with this boat.
Not so: they are actually planning on selling it to some poor sucker. Asking price: 277,000,000 Euros.
If that’s what they mean by “availability and proximity to us – our Lord”, then I’d say there might be just a wee bit of false advertising going on here.
The good news for the metal industry is that there seems to be a lot of money to be made in the construction of these monster yachts. Take note, folks: I appear to have stumbled upon an excellent target market for C Marshall Fabrication, as well as metal machinery outfits in general. Think of the amount of steel needed to construct a hull of this size!
The other good news is, I’m feeling a little more comfortable with my 39-foot sailboat.
-Anja Wulf
IndustryWeek (4/14) reports, “The results of the quarterly Manufacturers Alliance/MAPI Survey on the Business Outlook — March 2011 suggest a continued growth trend for manufacturing,” with an index reading of 72, this sixth month it has been above the 50 mark, indicating expansion. However, “the rate of growth may start slowing later this year.” Donald A. Norman, a MAPI economist and the survey’s coordinator, said, “The results of the March survey show the indexes to be strikingly robust and relatively stable. … As such, they paint a clear and consistent picture of continued growth in manufacturing sector activity.”
Manufacturing’s Strong Performance Sets High Expectations. Under the headline “US Manufacturers Face A High Bar This Quarter,” Reuters (4/15, Malone, Zieminski) reports that manufacturing’s strong performance in the past several quarters, when it has taken point in the US economic recovery, has created very high expectations from investors. “It’s easy to satisfy distraction and depression, but now things are better, companies have been reporting rising earnings and it’s harder to impress people,” explained Peter Klein of Fifth Third Asset Management. These heightened expectations are only one difficulty manufacturers must deal with; higher energy and input costs are also pressing on margins.
From SME Daily Executive Briefing 4/15/2011